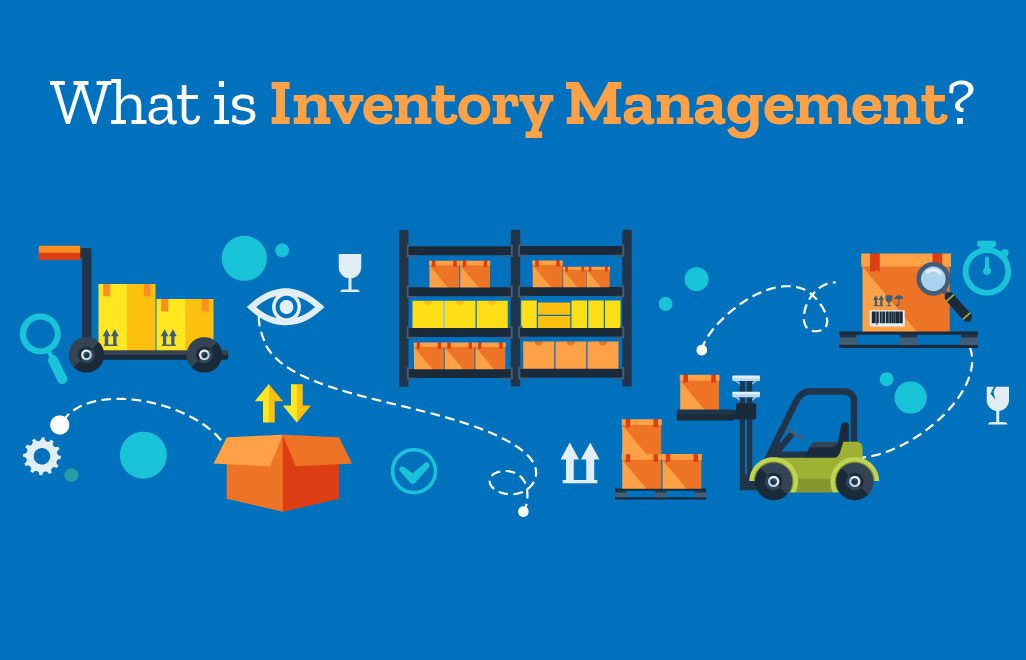
Running a successful power washing business isn’t just about showing up with a pressure washer and getting the job done — it’s also about having the right supplies on hand, knowing when to restock, and avoiding costly downtime due to poor planning. 🧠⏳
Let’s face it: nothing ruins a productive workday faster than realizing you’re out of surfactant, your hose coupler just snapped, or you forgot to bring enough bleach. Whether you’re a solo operator or running a small crew, inventory management can make or break your efficiency and professionalism.
In this article, we’ll dive into how to organize and manage your power washing inventory effectively — from essential gear and chemicals to replacement parts and restocking systems. 🗂️💼
🎯 Why Inventory Management Matters
Many small business owners overlook this area, thinking it’s only for large operations. But even if you’re just starting out, tracking your supplies and tools will help you:
- Avoid job delays or cancellations
- Reduce emergency hardware store trips
- Keep consistent service quality
- Control costs and reduce waste
- Scale your operations with confidence
It’s all about staying prepared and professional. 📋✅
🧽 What to Keep in Your Inventory
Let’s break down the essentials into three main categories: consumables, equipment, and parts/accessories.
🔹 1. Consumables (Used Regularly and Replenished Often)
These are the materials you go through on a daily or weekly basis — and running out can bring your operations to a halt. Make sure you always have:
- Sodium Hypochlorite (SH / bleach) 🧪
- Used for soft washing and killing organic growth
- Keep it fresh — SH breaks down quickly over time
- Surfactants 🧼
- Helps solutions stick and dwell longer
- Common brands: Elemonator, Green Wash, or homemade mixes
- Rust removers, degreasers, or specialty cleaners
- Optional, but essential for certain job types
- Pump sprayers and mixing containers
- PPE (gloves, masks, safety glasses) 🧤😷
🛒 Pro Tip: Buy in bulk when possible, but never let chemical stock sit unused for too long — especially bleach!
🔹 2. Essential Equipment (Daily Use Items)
These are the tools you rely on every day. Keep them in top condition and always ready to go:
- Pressure washer (gas-powered or skid)
- Surface cleaner (16–20 inch)
- Soft wash pump system
- High-pressure hoses (100–200 ft)
- Trigger gun and wands (various lengths)
- Nozzles: 0°, 15°, 25°, 40°, soap tip, turbo
- Ball valves, quick connects, and couplers 🔧
💡 Label or number similar tools so you can easily track wear, maintenance dates, or replacements.
🔹 3. Parts & Accessories (Spare and Emergency Items)
It’s not enough to just have your working gear — you need backups for the little things that always seem to break at the worst time. Keep extras of:
- O-rings and seals 🟤
- Hose fittings and quick connects
- Spare nozzles (they clog and get lost often)
- Pump repair kits or backup pumps
- Fuel cans and oil for engines
- Battery chargers (for 12V systems)
- Zip ties, Teflon tape, and thread sealant 🛠️
🧠 Think ahead: What would ruin your day if it broke on a job site? Keep two of those in your van at all times.
Browse Amazon Here For Top Rated Power Washers And Accessories
🗂️ How to Organize Your Inventory
A messy van = wasted time and lost tools. Here’s how to keep it under control:
✅ Label Everything
Use colored tape or permanent markers to label containers, jugs, hoses, and sprayers.
✅ Use Bins or Toolboxes
Group related items together:
- All fittings in one bin
- All PPE in one bin
- Separate bin for chemicals
🧰 Stackable plastic containers or contractor toolboxes work great in vans or garages.
✅ Create a Restock List
Tape a laminated inventory checklist to your trailer wall or shop door. At the end of each workday or week, do a quick scan and mark what needs restocking.
🗓️ Bonus: Use a whiteboard calendar for tracking supply runs or chemical orders.
✅ Implement a “Truck Restock” Routine
Just like restaurants do prep every morning, you should check your inventory before heading out. This 5–10 minute ritual prevents 90% of on-site issues.
📊 Tracking Inventory Like a Pro
As your business grows, manual systems get harder to manage. Consider these tools:
📱 Apps and Digital Tools
- Sortly – visual inventory tracker with photos
- Google Sheets – create a custom tracker for chemicals, parts, and usage
- Jobber or Housecall Pro – add notes for job-specific supply use
- Trello – use boards for restock workflows
🧑💻 Don’t overcomplicate it — even a basic spreadsheet helps you spot trends and prep for busy seasons.
💸 Budgeting for Inventory
Inventory eats up part of your monthly expenses, so build it into your pricing model. Here’s a rough breakdown:
- Chemicals and consumables: 5–10% of job cost
- Small parts and accessories: 1–3% of job cost
- Equipment repair/replacement: Budget monthly or per 100 hours of use
📈 Treat inventory as an investment, not an expense — because it directly supports your revenue.
🚨 Common Inventory Mistakes to Avoid
Here are a few inventory-related traps that catch many new power washers:
- ❌ Running your chemical supply down to the last drop
- ❌ Relying on memory instead of written lists
- ❌ Ignoring expiration dates (especially SH bleach)
- ❌ Forgetting to restock after big commercial jobs
- ❌ Not checking inventory before a multi-job day
Stay one step ahead — it’ll save you more time than you think. ⏱️🧠
🧽 Final Thoughts: Inventory Is a System, Not a Chore
When your van is stocked, organized, and ready for anything, you move faster, look more professional, and feel less stressed. Inventory isn’t just about tools and chemicals — it’s about building confidence and consistency in every job. 🚐💪
Here’s a quick recap:
✅ Track what you use regularly
✅ Stock extras of small, failure-prone items
✅ Organize your setup by category
✅ Create a restock routine
✅ Use digital tools to plan and forecast
✅ Build inventory into your job pricing
You don’t have to be perfect — just prepared. 📦🧽✅
Browse Amazon Here For Top Rated Power Washers And Accessories