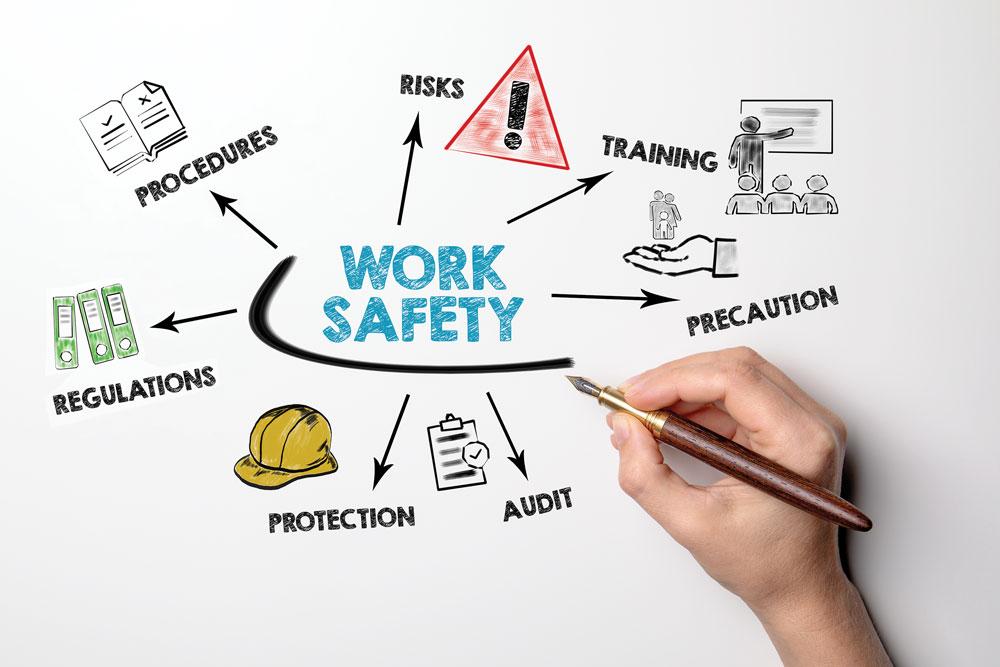
Running a power washing business is about more than just clean surfaces — it’s about keeping your crew safe and your clients happy. Power washers can reach pressures over 3,000 PSI, turning water into a potentially dangerous force. Without proper training, employees risk injury, equipment damage, and even legal trouble. 😬💦
That’s why a strong training program is essential. Teaching employees to power wash safely, efficiently, and professionally protects your team and enhances your business reputation. This article covers key training steps, safety protocols, and practical tips to help you create a workplace culture built on care, confidence, and compliance. 🧰✅
🧯 Why Safety Training Matters
⚠️ Power Washing Hazards:
- High-pressure water injuries (lacerations, bruises)
- Electrical shock (near outlets, fixtures, wires)
- Slips and falls from wet or elevated surfaces
- Exposure to harsh chemicals
- Damage to client property (paint, siding, glass)
Many of these risks are preventable with proper training. By teaching your team the right techniques, you’ll avoid:
- Costly equipment repairs
- Insurance claims or lawsuits
- Lost time due to injury
- Negative reviews from accidental property damage
Training isn’t just a box to check — it’s your front line of protection. 🛡️
🧑🏫 Step 1: Start with the Basics of Power Washing
Begin every training program with a strong foundation. Before employees ever touch a washer, they should understand:
💧 Power Washing Essentials:
- The difference between pressure washing and soft washing
- Common surface types and how they respond to pressure
- What PSI and GPM mean and how to adjust them
- Types of nozzles and spray patterns
- Environmental awareness: water runoff, landscaping, overspray
Use real-world visuals, short videos, or product demos to reinforce these concepts. 🎓📹
👷 Step 2: Teach Equipment Handling and Maintenance
Once they understand the basics, move on to handling the tools themselves.
✅ Include in Training:
- How to safely start and shut down the machine
- Proper hose setup and storage
- Adjusting pressure and nozzle types for different jobs
- Using extension wands and ladder safety
- Daily inspection checklist for wear, leaks, and hazards
Also teach the “why” behind each maintenance step. Technicians who understand how equipment works are more likely to respect and care for it. 🛠️🧽
🧪 Step 3: Cover Chemical Safety and Application
Many power washing jobs involve detergents, degreasers, or mold removers — and not all of them are safe for skin, lungs, or plants.
🚨 Chemical Training Topics:
- Understanding MSDS (Material Safety Data Sheets)
- Safe handling and storage of chemicals
- Mixing ratios and dwell times
- PPE requirements (gloves, goggles, respirators)
- How to protect landscaping, pets, and people nearby
Employees should know how to respond to chemical exposure, spills, or client concerns. It’s better to over-prepare than to scramble when something goes wrong. 🧪🚿🌿
🧍♂️ Step 4: Demonstrate Safe Washing Techniques
Now it’s time for hands-on training. Supervisors should walk each trainee through the proper washing technique for different surfaces:
📋 Practical Skills to Cover:
- Correct spray distance (usually 6–12 inches from the surface)
- Angle of application to prevent damage or water intrusion
- Proper pressure for surfaces like siding, concrete, wood, and windows
- Starting from bottom to top for pre-treatment, then rinsing top-down
- Checking weather conditions and adjusting for wind or rain
Use mock surfaces or real test areas. Give clear correction and praise — confidence grows with positive, specific feedback. 🎯💬
📋 Step 5: Emergency Protocols and On-Site Safety
No job site is 100% predictable. Training should prepare employees for sudden issues and emergencies.
🚑 Must-Know Protocols:
- How to shut off water and equipment quickly
- What to do if someone gets hurt (first aid, reporting, emergency services)
- Fire extinguisher location and use
- When to stop work due to unsafe conditions
- Dealing with aggressive dogs, wasp nests, or confrontational customers
Also cover proper signage, cones, or barriers to protect pedestrians and clients during commercial jobs. 🛑⚠️🦺
💼 Step 6: Train for Professionalism and Customer Service
A clean jobsite is only part of the client experience — how your crew interacts with customers matters just as much.
🗣️ Teach Soft Skills Like:
- Arriving on time and in uniform
- Respecting client property (don’t drag hoses over flowers!)
- Communicating delays or issues professionally
- Explaining what they’re doing in simple terms
- Asking for feedback or reviews post-job
Even the best washer in the world won’t earn return business if they’re rude or careless. Great service builds trust and long-term relationships. 💬🤝
🧪 Ongoing Training and Certifications
One-and-done training isn’t enough. Continue developing your crew with:
- Monthly refresher sessions or toolbox talks
- Safety quizzes or demonstrations
- Certification through PWNA, OSHA, or local programs
- Cross-training for new services or equipment
- Mentor programs where veterans teach new hires
The goal is to build a team that’s confident, consistent, and safety-focused. 📚🏆
✅ Final Tips for Effective Training
- 👂 Listen to feedback from field workers — they often spot hazards first
- 📷 Use job photos or videos to show both good and bad practices
- 📋 Create laminated checklists or cheat sheets for crews
- 🎓 Train in small groups for more interaction and hands-on practice
- 🎖️ Recognize employees who model safe behavior — reward excellence!
💬 Final Thoughts
Training your employees in safe power washing practices is an investment that pays for itself. It lowers your liability, protects your equipment, and elevates your customer experience. Most importantly, it ensures everyone on your team goes home safe at the end of the day. 👷♂️💧
A well-trained employee isn’t just a better worker — they’re a brand ambassador, a safety leader, and a valuable asset to your company’s future. So take the time to train right, and you’ll build a business that lasts. 💪🧼💼
Browse Amazon Here For Top Rated Power Washers And Accessories